The FT5 Powder Rheometer quantifies dynamic behaviour by measuring the resistance to movement of the blade through the powder sample. Capturing both Torque (rotational resistance) and Force (axial resistance) is critical to accurately quantify a powder’s total resistance to flow.
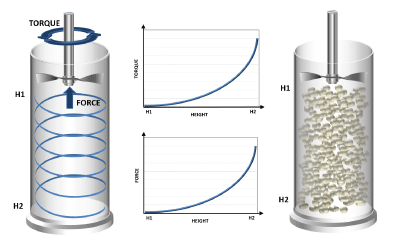
Torque and force signals are combined to calculate Total Flow Energy, the energy required to traverse the blade through a fixed sample volume. Since the values of torque and force change continuously, as the blade advances through the powder column, total energy is calculated for each small distance travelled. This produces the Energy Gradient curve, a plot of total energy for each millimetre of blade travel, expressed in mJ/mm, as a function of bed height.
The area under the Energy Gradient curve quantifies the Total Flow Energy, the powder’s resistance to flowing in a specific regime.
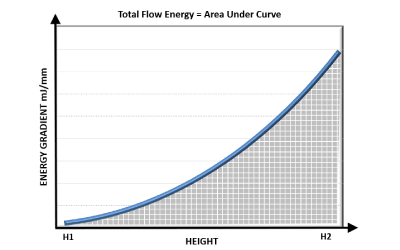
Energy Gradient is calculated directly from measurements of Torque and Force
Work Done = Energy = (Resistance x Distance travelled)
where ‘Resistance’ is the combined Torque and Force
Energy Gradient = total energy per mm of blade travel
Confined and Unconfined Powder Flow
The FT5 applies two different dynamic regimes to quantify powder flow properties: -
Forced (or confined) Flow
Basic Flowability Energy, BFE is a measure of the powder’s flowability when forced to flow, such as through a screw feeder or in an active feed frame. BFE is measured during the downward blade movement when the powder is confined by the closed base of the test vessel.
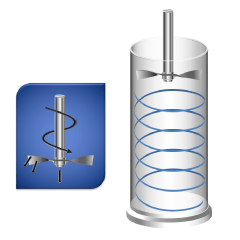
Direction of movement downwards
Low Stress (or unconfined) Flow
Specific Energy, SE is a measure of the powder’s flowability when unconfined, such as during low stress filling, or low shear blending. SE is measured as the blade traverses from the bottom of the vessel to the top. As there is no solid surface at the top of the vessel preventing the powder from dilating and moving upwards, the powder is unconfined during this test.
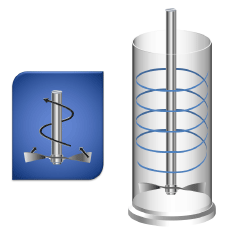
Direction of movement upwards
The regimes of confined and unconfined flow are very different and so it is important, when correlating data with process performance, to identify which regime is most representative of the process being considered.
Bulk properties are not a direct measurement of flowability or shear, but nevertheless influence process performance and product attributes. The FT5 Powder Rheometer® measures three bulk powder properties: -
Density
Density defines the relationship between mass and volume. In principle this seems a simple concept, but the nature of powders means that their packing structure can change easily and significantly. Therefore, when defining density, it is essential to ensure the packing state is well known and reproducible. The FT5 uses a Conditioning cycle to meet this goal. In combination with other features such as the integrated balance and the Split Vessel design, which allows a precise volume to be attained, this step ensures Conditioned Bulk Density can be measured with unprecedented levels of accuracy.
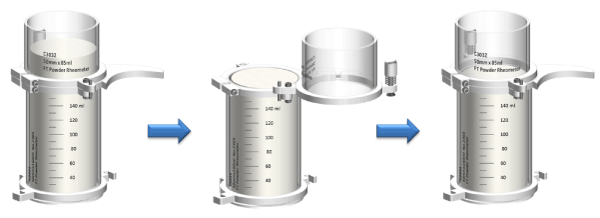

Compressibility
Compressibility is measured by applying increasing levels of compressive force to a conditioned powder and measuring the change in volume as a function of the applied load. Use of a Vented Piston to apply force ensures that air trapped within the powder can readily escape. The high-resolution position measurement system is also critical for the precise quantification of Compressibility, which is expressed as a percentage change in volume for a given applied normal stress.
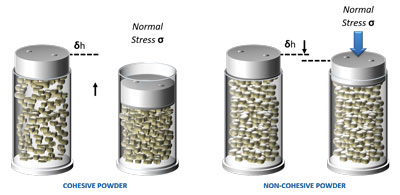
Compressibility = percentage change in volume after compression (%)
The data generated in compressibility measurements can also be expressed as a Compressibility Index or as Bulk Density, both as a function of applied normal stress.
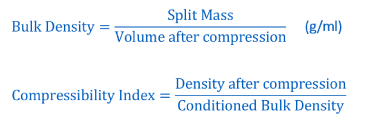
Permeability
Permeability is a measure of the powder’s resistance to air flow. Not to be confused with an Aeration test, this method utilises the Vented Piston to constrain the powder column under a range of applied normal stresses, as air is passed through it at a known flow rate. The pressure drop across the powder column is a function of powder permeability. Tests can be completed under a range of normal stresses and at different air flow rates.
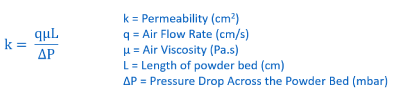
This important material property is relevant in many applications, including tabletting and filling, for example. In a tabletting process, the efficiency of air removal during the compression step influences the mechanical properties of the compact; air retention within the tablet, due to low powder permeability, is associated with capping or lamination. Within a filling application, the ability of the air to “back flow” out of the die or container through the inflowing powder depends on bulk permeability which therefore influences fill rate and fill consistency. Whilst permeability is a relatively simple bulk property, it is important in many processes and applications making accurate measurements highly valuable.
Shear Cell
The FT5 Powder Rheometer® also incorporates Shear Cell functionality for the measurement of shear properties in accordance with ASTM D7891. Shear testing is a quasi-static technique, quite different to dynamic testing, that characterises powders in a consolidated state and quantifies the ease with which that consolidated powder transitions from a static to dynamic state.
Shear cells are ideally suited to predicting powder behaviour in process operations where the powder is consolidated and where flow rates are low and / or sporadic. They have been successfully applied for understanding powder behaviour in hoppers and provide the key data needed for hopper design (based on the Jenike stress theory developed during the last century).
Operating Principle
In shear cell testing, a shear (or horizontal) force is applied at very low speeds to an upper layer of powder whilst the adjacent lower layer is kept stationary (or vice versa). The applied shearing force is increased to the point at which it is sufficient to overcome the powder’s shear strength, at which point the bed ‘yields’ with the upper layer of powder slipping relative to the lower.
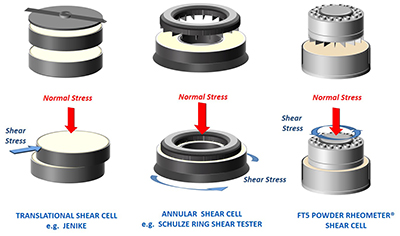
Several types of shear cell design have emerged over the last 50 years, each employing this same concept. Rotational designs are most frequently in use today. These offer the advantage of allowing the two layers of power to be sheared relative to one another over a large distance, in contrast to translational designs that quickly exhaust their range of displacement.
In a typical shear cell test sequence, tests are carried out at different levels of normal stress. The data produced capture the relationship between shear stress and normal stress, and can be plotted to determine the powder’s Yield Locus. In simple terms, the higher the shear stress for a given normal stress, the less likely it is that the powder will yield and begin to flow when confined under a similar consolidation stress in a hopper or other vessel.
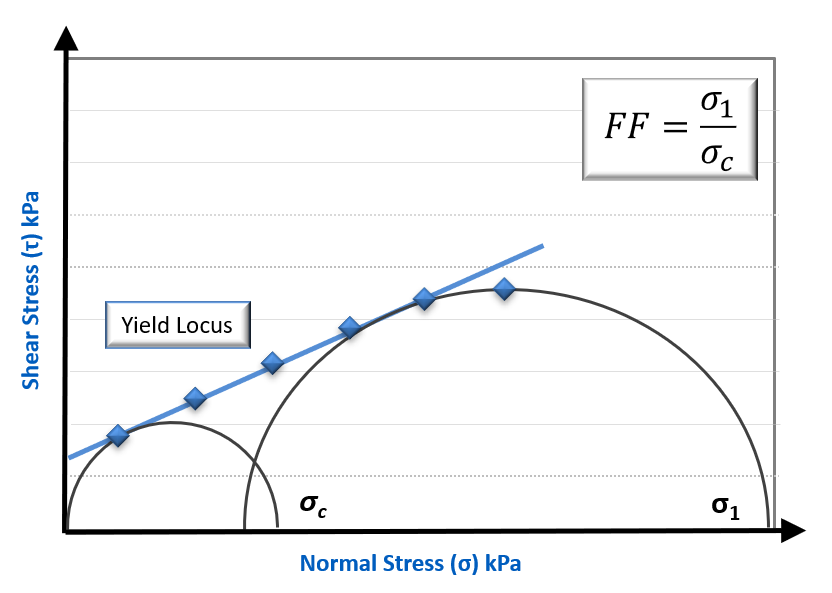
It is possible to apply a number of mathematical models to this data, but it is important to consider that in doing so, trends may be exaggerated or reduced. Fitting Mohr’s Circles to the yield locus identifies the Major Principal Stress (σ1) and Unconfined Yield Strength (σc), and the ratio of these properties quantifies the Flow Function, FF. Flow Function is a parameter commonly used to rank powder flowability.
Wall Friction
The Wall Friction test provides a measurement of the sliding resistance between the powder and a specific material. This is particularly important for hopper design calculations and more generally for understanding interactions between a powder and processing equipment to elucidate, for example, the continuity of flow in transfer chutes and tablet ejection forces. Wall friction data are also useful when investigating whether a powder will adhere to the wall of process equipment and various other surfaces, such as the inside of sachets, capsules, and other packaging material.
The measurement principle is very similar to the shear cell test, but powder is sheared relative to a test coupon representing the process equipment wall rather than another powder. The FT5 Wall Friction accessory allows for investigation of a range of material finishes and bespoke materials can be easily added.
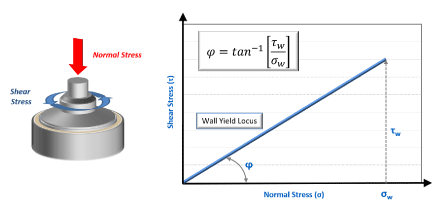
Data are typically represented as a plot of shear stress against normal stress, allowing the determination of Wall Friction Angle (ϕ). The higher the wall friction angle, the greater the resistance between the powder and coupon.
Hopper Design
Hoppers are used extensively throughout industry and whilst often considered to be simple systems, are renowned for causing process interruption and product quality issues.
If powder properties are incompatible with a specific hopper geometry and material of construction, then flow from the hopper may be inconsistent or even non-existent. However, since the pioneering work of Andrew Jenike in the mid twentieth century, it has been possible to utilise data from shear cell and wall friction tests to calculate the critical hopper dimensions to ensure good flow. Even today this methodology remains the only well-established, fundamental design technique for powder processing equipment.
The FT5 comes with fully automated hopper design software, which takes results directly from shear cell and wall friction tests into the hopper design algorithms. The result is a fully automated hopper design exercise in less than 3 hours.

Please contact us for more information on the hopper design process, if required.
The Need for Versatility
The diversity and complexity of powder flow behaviour cannot be quantified by a single number but should rather be considered in relation to the conditions imposed by the process and application. Powders may exhibit “good” flow if loosely packed, but “bad” flow after consolidation. Some powders may flow well at relatively high flow rates but may stop flowing when moved more slowly.
The FT5 Powder Rheometer has been designed to allow comprehensive investigation of the effect of external variables. By closely simulating process conditions in the measurement cell, the powder’s response to each variable can be quantified.
External variables include:
- Conditioning
- Aeration
- Flow (Shear) Rate
- Moisture
- Electrostatic Charge
- Storage Time
Using Dynamic Methods to Quantify the Effects of External Variables
BFE is a measure of a powder’s flow properties when the powder is in a loosely packed state (following Conditioning) and subject to forced flow conditions. Using this same dynamic methodology, and taking BFE as a baseline, it is possible to quantify how powder flow properties change as a result of changes in external variables.
Aeration
To quantify the influence of air, a controlled air supply is introduced through a porous mesh at the base of the powder column. This method not only simulates processes and applications where air is intentionally introduced into the powder, such as conveying, drying and in dry powder inhaler usage, but more generally quantifies the strength of inter-particular cohesive forces.
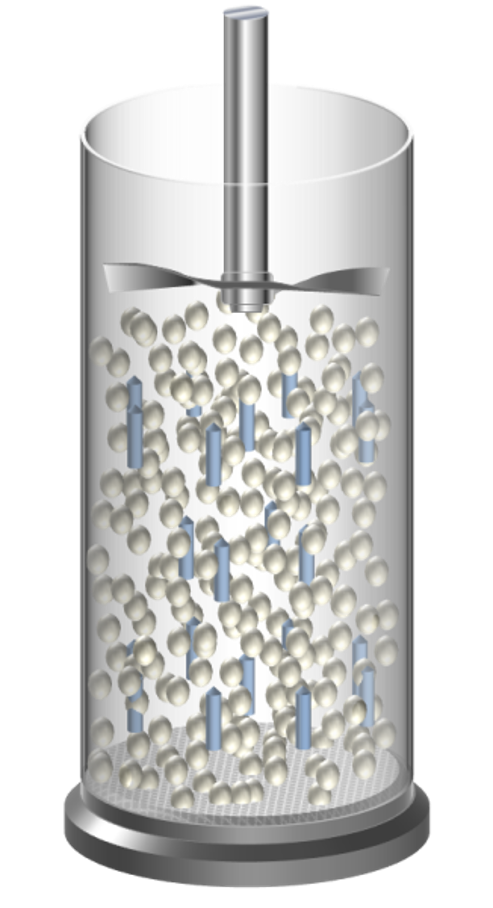
Air In
Aeration Test
Cohesive forces are notoriously difficult to measure but can be accurately and directly quantified by assessing how aeration changes the flow properties of the bulk powder. Cohesive forces are a combination of Van der Waal’s and electrostatics, and act to “bond” particles together. Air flowing up through the powder column will tend to separate adjacent particles, overcoming these cohesive forces. If the forces are weak, each particle will separate from its neighbour and the powder will fluidise. The measured resistance to flow, the Aerated Energy, AE, for an aerated sample therefore quantifies the strength of the cohesive forces.
For powders with weak cohesive forces, AE tends towards zero as the powder becomes fully aerated. Powders with moderate to high cohesion will exhibit a reduction in flow energy when aerated, but to a much lesser extent. In cohesive powders, the tensile forces are too strong for the air to overcome and the particles do not separate. Instead, channels are established in the powder through which the air passes. AE values therefore remain relatively high, even at high air velocities.
Comparing BFE with AE generates an Aeration Ratio, AR, where:
ARx= = BFE / AEx
and ‘x’ defines the air velocity in mm/s at which the AE measurement is taken.
AR quantifies a powder's sensitivity to aeration.
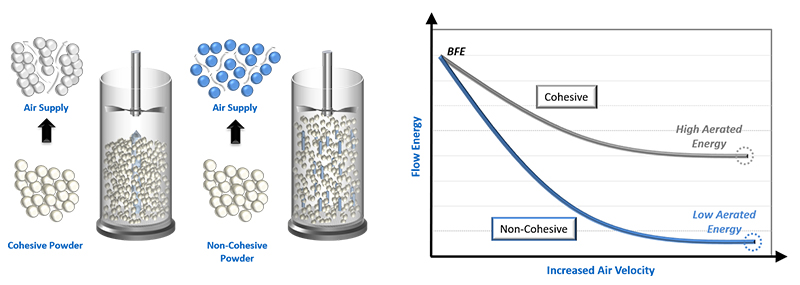
Consolidation
The effect of consolidation on powder flow properties can be directly quantified by the Consolidation Energy, CE. This is a very similar test to that used to measure BFE but uses a powder sample that has first been subjected to consolidation. Following a Conditioning cycle, to generate a uniform packing density, the powder is typically subjected to a number of taps, in order to induce consolidation prior to measurement.
It is also possible to consolidate the powder using an applied normal force. This compaction technique more closely simulates the effect of storage, in contrast to behaviour during transport or in other environments where powders are subjected to vibrational consolidation. With either consolidation method, the powder is consolidated before the flow energy, CE, is measured.
Comparing CE with BFE generates a Consolidation Index, CI where:
CIx = CEx / BFE
And ‘x’ defines either: -
- The number of taps, or
- The applied normal stress during compaction (kPa)
CI quantifies the change in powder flow properties as a function of consolidation and is a measure of the powder’s sensitivity to consolidation.
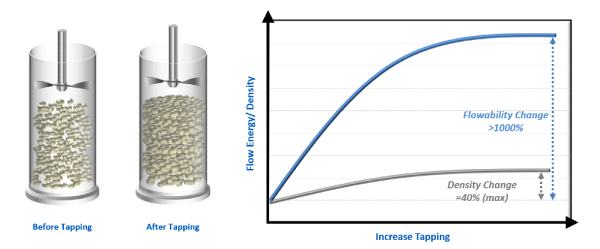
Traditional tapped density methods, such as Carr’s Index and Hausner Ratio, seek to define certain aspects of powder flowability based on a volume change, as a result of tapping the sample. As the graph above illustrates, changes in density may be as high as 40%, however flowability may actually have changed by 1000% as a consequence of tapping. The direct measurement of CE quantifies that flowability is in fact 10 times worse after tapping and illustrates why inferring flow characteristics from density measurements is often misleading. After all, from a processing and application perspective, the interest is mostly to determine whether the product will flow, rather than whether its density has changed.
Flow (Shear) Rate Sensitivity
Powders typically exhibit different behaviour when moved at different flow rates. This means that they may flow freely at one speed and badly at another. This sensitivity to changes in flow rate has a number of implications for powder processes, particularly blending and mixing operations, and can seriously effect process stability.
Powders with high flow rate sensitivity require an optimised and specific mixing configuration to attain blend uniformity and are more likely to require high shear processing. In contrast, powders with low flow rate sensitivity are more amenable to low shear mixing operations that minimise the risk of particle attrition and electrostatic charge evolution.
Unlike many liquids, powders are rarely Newtonian in nature, exhibiting a complex behavioural relationship with the speed at which they flow. In fact, it is common that powders are more difficult to move at lower speeds than at higher velocities, which means blockages may occur should flow rates drop below a critical value.
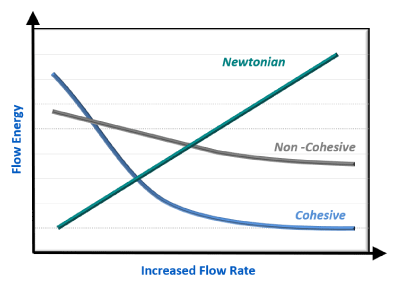
Utilising the dynamic methodologies of the FT5 Powder Rheometer, and good experimental design, it is possible to investigate a number of other behavioural properties of powders, including:
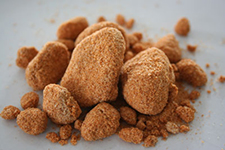
Caking
Powder consolidation with time
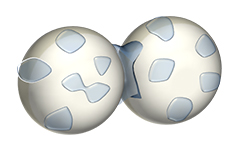
Moisture
The influence of free moisture on the behaviour of the powder
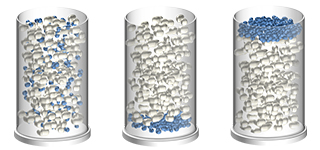
Segregation
The potential for particles to rearrange according to their size / density
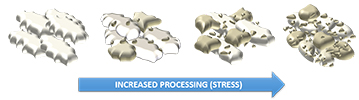
Attrition
Particle friability, resulting in changes in particle size, shape and surface area
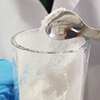
Electrostatics
Changes in behaviour as a function of electrostatic charging
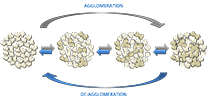
Agglomeration
The formation of agglomerates from primary particles, usually as a function of being processed