Powder Rheology
Powder rheology is the study of the behaviour of powders as bulk assemblies, consisting of solids, liquids and gases. It allows users to measure the dynamic flow and shear properties of powders as well as quantifying bulk properties such as density, compressibility and permeability.
Powder rheology is used in a wide range of industries to support new product development and manufacturing. By investing in powder rheometer, manufacturing sites can establish an understanding of their processes and unit operations based on a correlation between measurable powder properties and process performance.
Why are Powders Complex?
The Three Phases of Powders
Whether as raw materials, intermediates or final products, powders are integral to a huge range of industrial processes, contributing to some 80% of all manufactured goods. However, despite their ubiquity they continue to present challenges during product development, manufacturing, and in quality assurance. Often powders are labelled as ‘bad’, when it would be more accurate to say we simply don’t understand how they are behaving. A good understanding of powder rheology, or powder behaviour, is an essential foundation for optimising production processes and developing a high-quality product. The sections that follow, introduce the challenges associated with predicting powder flowability and how understanding powder behaviour can benefit process performance.
Powders are more than just particles alone, they are unique materials consisting of three distinct phases. They comprise solids in the form of the particles, air between the particles, and often water on the surface of, or within the particle.
Powders are bulk assemblies consisting of solids, liquids and gases
There is a common misconception that powder behaviour can be described by just understanding powder flowability and that flowability is a discrete property that can be quantified with a single number.
Unfortunately neither of these assumptions are correct, which explains why well into the 21st century we still do not possess a fundamental understanding of powder rheology. Consider a loosely packed powder in a glass jar and visualise its behaviour whilst the jar is tumbled. Then consider how differently it would behave if the jar was first tapped a number of times on a hard surface. Any differences in behaviour from a loosely packed state to a tapped state would be due to the characteristics of the powder. If the powder was dry sand, then it would behave in a similar way before and after tapping. However, if the powder were flour for example, it would flow very differently after it had been tapped. This is an important characteristic and one very typical of powders.
Particle properties are important when it comes to powder behaviour but so too are external variables such as the extent of aeration or consolidation
In each state illustrated above, the physical and chemical properties of the particles are the same, but the way the powder flows is very different, simply as a result of changing the air content and contact stresses between the particles.
The Influence of External Variables
As illustrated in the previous example, powders can behave very differently when they are fully aerated, loosely packed or consolidated. Some powders are extremely sensitive to these variables whilst others less so. A given powder could flow well when aerated and loosely packed, but become a real problem if consolidated (toner, for example). A different powder could exhibit reasonable flow properties when loosely packed, not be too affected by consolidation, but show real improvements in flow properties following aeration. Considering this observation, it seems unlikely that a single number can be used to fully quantify powder flowability, or describe a powder’s response to the large range of aeration and consolidation levels that the powder will experience during processing and application.
The extent of consolidation stress and air content are two of the most influential variables as far as flow properties are concerned. However, powder behaviour and powder flowability is also affected by the speed at which it is processed, such as during mixing or when on a filling line for example, as well as by other variables such as ambient moisture level and storage time. A powder that was once performing well may exhibit poor behaviour if left in storage, or if processed in an environment with slightly higher humidity than normal.
External Variable
|
When and Where
|
Effect
|
Consolidation
|
Vibration / Tapping
Direct pressure (hopper, IBC, keg)
|
Increase in particle pressure, contact area and number of contact points
Reduction in air content between particles (reduced porosity)
|
Aeration
|
Gravity discharge
Blending
Pneumatic conveying
Aerosolisation
|
Reduction in particle pressure, contact area and number of contact points
Increase in air content between particles (increased porosity)
|
Flow (shear) Rate
|
Within powder
Powder against equipment wall
Mixing
|
Mostly non-Newtonian
Greater resistance to flow at lower flow rates
|
Moisture
|
Storage
Processing
Intentionally introduced
(granulation)
|
Increase particle adhesion
Reduces particle stiffness - more compliant but increased contact surface area
Increase electrical conductivity
|
Electrostatic Charge
|
Discharge from hopper
Pneumatic conveying
High shear mixing
|
Increase bond strength between particles
Adhesion of powder to equipment
|
Storage Time
|
Raw materials / intermediates
|
Consolidation
Caking
Permanently affecting downstream performance
|
Controlling certain variables may be relatively straight forward, but changes in air content and consolidation stress is usually unavoidable during processing. Even the most basic of transfer chutes has the potential to aerate and consolidate the powder moving through it. Aeration occurs as a powder dilates, with particles becoming further separated, and this occurs in many processes, including blending, filling and discharge operations, even though an external air supply is not being applied, as it would be in pneumatic conveying.
Recognising that any of these external variables has the potential to change the way the powder behaves is the first step in gaining a better understanding of process performance. Measuring a powder’s response to each external variable then provides the ability to understand powder rheology, i.e. why a powder behaves in a certain way, and the chance to optimise both formulation and manufacturing efficiency.
The Influence of Particle Properties
In addition to external variables, there are a number of particle properties that contribute to powder flowability and bulk powder behaviour. Particles are complex, yet never described by an adequate set of parameters in terms of their specification. Particle size and size distribution have traditionally been considered, and they remain important, but in fact there are many particle properties that will influence the overall behaviour of the powder. Important particle properties include:
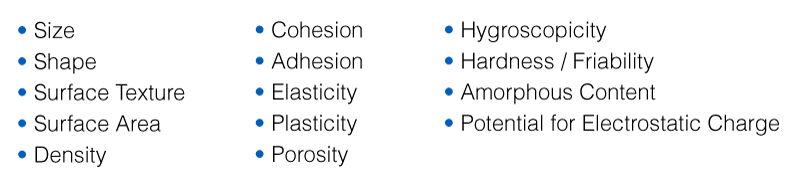
Note that many of these properties are also distributions, rather than a single value.
Some properties can be measured directly, whilst others are more challenging to quantify. However, all have the potential to contribute to the way the powder behaves.
When considering the number and diversity of particle properties and external variables, it becomes clear why a mathematically and fundamental approach to predicting powder behaviour is very difficult, if not beyond our current capability.
Mechanisms of Particle Interaction
Further insight into the behaviour of the bulk powder can be gained by understanding the mechanisms of interaction that exist between particles. There are a number of effects that contribute to the ease of movement of one particle relative to another. Understanding each effect, and how they can be engineered to work to our advantage provides great opportunity in both product development and process optimisation.
Mechanisms that restrict particle movement:
Friction
Particles with a smoother surface will generally have a lower frictional interaction and flow more easily than those that are rougher, assuming all other features are identical.
Mechanical Interlocking
Particles of a certain shape can mechanically interlock and resist flow.
Inter-particulate forces of cohesion
Inter-particulate forces act between contacting particles, and those in close proximity.
Liquid Bridging
Liquid has the ability to bridge between particles, creating capillary bonds and reducing particle independence.
All mechanisms above act to restrict particle-particle independence, and generally speaking, the stronger their influence, can result in poorer powder flowability. However, powders with high levels of cohesion, irregular morphology and high surface friction still can be observed to flow, so there is clearly a significant motivating force that causes particles to move.
Mechanisms that promote particle movement:
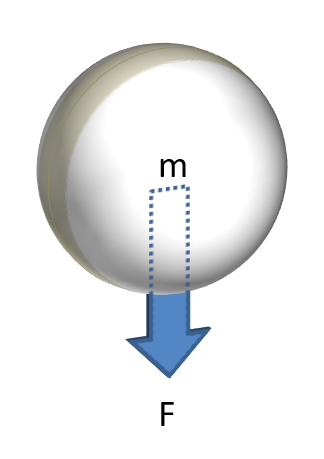
F = mg
Gravity
Gravitational forces are often the only motive force acting on the particle.
Ignoring for a moment that particles in motion will have inertia, the primary motivating force acting on a loosely packed stationary particle is that due to gravity - its weight. Therefore, the ability of a particle to begin to flow is largely dependent on the strength of the gravitational force acting on it. It is for this reason that powders containing particles of a large size, or consisting of material that has a high density, tend to flow better when loosely packed, as the particle's individual mass, and therefore the gravitational force acting on it, is high.
The behaviour of the bulk powder is influenced by all mechanisms of particle interaction. However, the influence of each will depend on the properties of the powder and the environmetal / process conditions imposed.
The force relationship between all restrictive forces and the motivating force of gravity is what determines whether particles can move independently or whether they will exist as part of an agglomerate. In the latter case, bulk flow is influenced by the mass of the agglomerate and its relationship with surrounding agglomerates.
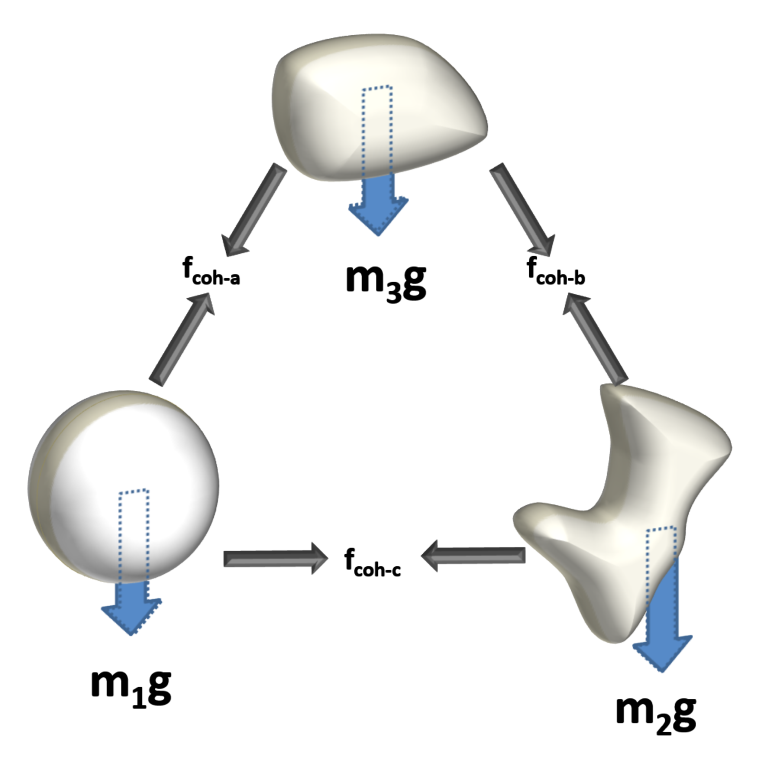
There is a common misconception that powders with small particle size have stronger cohesive forces, but this is not necessarily the case. Here, the gravitational forces acting on the particle are small because the individual particle mass is low, and hence the relative size of the cohesive force to the gravitation force is high, even though the absolute value of cohesive force could be low.
A powder consisting of mostly spherical particles will be optimised in terms of its dependence on particle shape. Therefore, changing properties like particle surface texture, extent of lubrication, moisture content, or the true density of the material will yield a strategy for optimising the properties of the bulk powder. A powder that is very cohesive may flow better if its free moisture content is increased, as the additional water on the surface of the particles acts as an electrical conductor and allows for some of the cohesive force to be dissipated. However, too much free moisture may result in capillary bonding between particles and flow will be compromised by the increased particle - particle adhesion.
The influence and importance of each mechanism also needs to be considered in regard to the process environment and the conditions to which the powder is being exposed. When powders are loosely packed, the cohesive forces are at their most influential, dictating the independence of each particle from one another. However, whenever the powder is consolidated, such as in a hopper or a feeder, the frictional forces and those due to mechanical locking are far more dominant, due to the fact that the particles are forced together. Under these circumstances, the number of contact points, the contact pressure, and, depending on the compliance of the particles themselves, the contact area, will increase. Cohesion still exists, but only represents a fraction of the forces that restrict independent particle - particle movement.
Understanding the interplay between the mechanisms of particle interaction and the conditions imposed by the process or application is a key step in optimising a formulation or process. Cohesive powders can be processed efficiently if the process design and configuration is optmised for a cohesive powder. Indeed, a less cohesive powder may perform poorly in the same process. Efficient powder processing is not about engineering the least cohesive powder, but about optimising the characteristics of the powder for the process or application of interest.
Learn more about Working with Powders