Quantifying the Impact of Powder Properties on Pharmaceutical Powders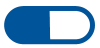
Powder processing lies at the heart of pharmaceutical manufacture. It is therefore necessary that efforts to improve efficiency and preserve quality must focus on understanding and controlling powder behaviour. Powders can be challenging to process efficiently, and indeed to characterise reliably, largely because their properties are affected by so many different variables.
When it comes to effective powder characterisation for process-related investigations, it’s imperative to apply methods that are not only reliable and reproducible, but which also generate data that is measured under the same conditions of stress and strain that the powder experiences in the process environment. The complexities of powder characterisation are reflected in the variety of techniques available and there is increasing recognition that in order to fully understand powder behaviour, a multifaceted approach, which examines a diverse range of powder properties, is required.
Below we look at a range of case studies which highlight a variety of processing challenges, and how powder testing can identify properties to optimise pharmaceutical processes.
|
Take a look at our new Pharma eBook
The 𝗣𝗵𝗮𝗿𝗺𝗮𝗰𝗲𝘂𝘁𝗶𝗰𝗮𝗹 𝗜𝗻𝗱𝘂𝘀𝘁𝗿𝘆 was the first to embrace the FT4 Powder Rheometer® and examples of the resulting rewards are numerous. Our new eBook discusses the application of dynamic, shear and bulk powder testing from formulation through process development to QC and troubleshooting!
You can view the eBook here.
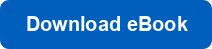
|
Case Study 1 - Continuous Manufacturing using High Shear Wet Granulation
Wet granulation is a process frequently employed during the manufacture of oral solid dosage forms. The objective is to convert the often fine and cohesive active ingredient and excipients, into more uniform, free-flowing granules that are optimised for downstream processing. Granules that possess ideal properties result in efficient process operation, including high throughput and tablets of the desired critical quality attributes (CQAs). However, this means that the granules produced by wet granulation are typically an intermediate, rather than end product, which raises the question of how to control the granulation process to achieve granules that ultimately make good tablets. In the first instance, it is necessary to identify measurable parameters of the wet granules that can be used to quantify differences in granule properties.
A study was carried out by Freeman Technology (FT4 Powder Rheometer®) and GEA Pharma Systems (ConsiGma™ 1) to determine whether the dynamic flow properties of granules from a wet granulation process could be correlated with tablet hardness, a common critical quality attribute of tablets. The results obtained demonstrate how the properties of finished tablets can be predicted from upstream measurements of dynamic flow properties of the wet granules.
You can download a copy of the application note at the bottom of the page.
Case Study 2 - Die Filling
Filling is a common operation across all industries, although fill weights and tolerances vary widely. The pharmaceutical industry often requires milligram doses to be filled accurately and at high speed, in order to meet the stringent criteria and high throughput requirements of tablet manufacture.
The factors that influence filling efficiency will depend on the type of equipment being used. In many applications, such as tablet manufacture on a rotary press, the powder fills the dies through a combination of gravity and force-fed flow. The influence of each of the two mechanisms will depend on the geometry and design of the feedframe, its operational speed in relation to turret speed, die geometry and the characteristics of the powder. It is easy to see, with wide variation in each of these variables that this is a complex process and remains challenging to model from knowledge of a limited number of particle properties and process parameters.
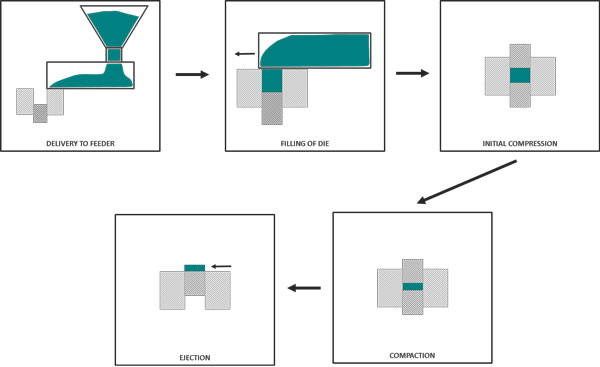
In this example of a simplified die filling process, the filling “shoe” moves relative to the stationary die, as opposed to the die moving underneath the feedframe, as in a rotary tablet press. There are many geometries and configurations, but in all cases there is a common objective – to fill the die in a homogeneous manner, in a time frame that enables the target throughput to be achieved.
Several mechanisms of particle interaction will strongly influence filling efficiency – cohesive forces, friction, particle interlocking and permeability. The example below shows a die filling process that involved a shoe containing powder moving at a controlled velocity relative to a fixed die. Filling Ratio was calculated as the mass of powder in the die after filling, compared to the mass if the entire volume of the die had been filled with a material of the powder’s bulk density. A ratio of 1.0 represents complete die fill, whilst a value of 0.2 indicates that only 20% of the die has been filled.
Download a copy of ‘Developing a Design Space for a Die Filling Operation’ at the bottom of the page.
Case Study 3 - Predicting Flow Performance in Screw Feeders
In powder handling industries, screw feeders are routinely used to control the flow of material from a hopper into the subsequent stage of a process. The accurate and consistent feeding of materials into blenders and other processing equipment is necessary to maintain optimal conditions, and to generate products of the required quality at the required rate.
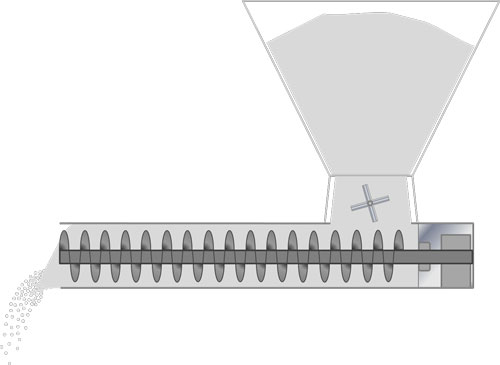
However, predicting feed rates has historically relied on engineering estimation based on experience or from pilot scale trials. This approach can lead to equipment that does not meet the target design requirements, and result in sub-standard operation and poor control of metered product.
In an attempt to more accurately predict the expected feed rate of powder in a given feeding process, one approach is to use statistical, multivariate models to evaluate the relationships between measured powder properties and process performance. However, many studies are hampered by the use of overly simplistic characteristics of the bulk powder, such as angle of repose, or flow through an orifice, which do not necessarily represent the conditions that the powder is subjected to in the feeder. A method of accurately quantifying a powder’s response to process-relevant conditions is required for the development of a robust statistical model.
A study between Freeman Technology and Gericke was conducted which describes new collaborative research to establish predictive correlations for the volumetric flow rate delivered by screw feeders, using dynamic powder testing, which can be used to accelerate and optimise screw feeder selection (download a copy at the bottom of the page).
Case Study 4 - Developing Generic Dry Powder Inhaler (DPI) Formulations
Dry Powder Inhalers (DPIs) are used to deliver a controlled dose of active pharmaceutical ingredient (API) to the deep lung. An excipient is employed to transfer the fine particles of the API from the device, before being trapped in the throat and subsequently swallowed, leaving the detached API particles to continue to the lungs.
Quality by Design (QbD) is encouraging the pharmaceutical industry to gain sufficient knowledge to specify, formulate and manufacture more effectively than it has in the past. Widespread interest in pulmonary drug delivery means that for many researchers, this involves a detailed understanding of relatively new technologies, such as dry powder inhalation.
DPI performance will be dependent on several powder properties, including the response to aeration, permeability, inter-particular mechanical locking and friction. By measuring the rheological properties of DPI formulations, the properties of the powder can be optimised for the device design and delivery mechanisms employed.
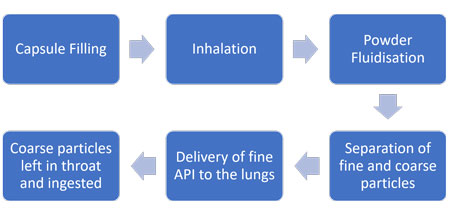
It is also important that the capsule or blister filling method is optimised for the properties of the DPI formulation, as problems here could lead to variation in performance, out of specification dose weight and issues that compromise stability and efficacy.
Addressing these issues requires an understanding of the mechanisms that contribute to successful drug delivery along with the ability to quantify the relevant properties. Many characterisation tools aren’t able to measure diverse aspects of behaviour, in particular the response to the introduction of air. The FT4 Powder Rheometer is unique in its ability to characterise aeration and fluidisation behaviour and this makes it a key tool for understanding and controlling dry powder performance.
For more details please download a copy of the study below.